what is Aluminum alloy Cold Forging?
What Is The Aluminum Cold Forging Process and AL Cold Forging Parts?
What is Cold Forging?
The most obvious difference between hot forge and cold forge is, while hot forge induces extensive heat onto the aluminum billet, cold forge simply keeps the workpiece at room temperature with no additional heating required. Cold forged products reach greater hardness yet lower malleability, however, this method is more cost- effective and more eco-friendly.
Why Cold Forging?
Cold forging is often preferred by manufacturers since it requires little to no finishing work. Considering that all workpieces are annealed before forging, it wouldn’t be necessary to apply an additional heating process before machining. The weight of the final product is equivalent to the original weight of the billet, no additional weight loss during cold forging. Cold forging also provides great dimensional precision, which is very suitable for small components. The shortened manufacturing time and longer lifespan of the die along with the advantages listed above, prompted many manufacturers to adopt cold forging into their production.
Due to not heating up the workpiece, the billets being worked during cold forging will be way harder and rather low in malleability, the stretch and shaping of the billet will be limited, therefore, customized designs can’t be produced by cold forging.
Due to not heating up the workpiece, the billets being worked during cold forging will be way harder and rather low in malleability, the stretch and shaping of the billet will be limited, therefore, customized designs can’t be produced by cold forging.
According to the statements listed above, only a few limited options of raw metal can be used to cold forging, for example: metals with a high carbon content won’t be appropriate for cold forging by reason of the low ductility nature of said metal, and might chip off or even break the material during forging.
How to Cold Forge?
The process of cold forging is performed under room temperature, hence the name, cold forging. The workpiece is simply pressed between an upper and lower die until it has formed the predetermined shape. To complete a cold forged product, it has to go over numerous procedures in order to finish, rolling, drawing, pressing, spinning, heading, and extruding. Cold forging extrusion is a very common way of manufacturing, this technique is widely used on automotive components.
Potential Cost Reductions in Hot Forging
To reduce cost in manufacturing cold forging products, the most direct way is raw materials, purchase them from upstream suppliers, eliminate the middle man and have metal workpieces sent right to the factories.
Also, obtaining professional know- how on all involved materials, tools, methods, and processes, distribute the fitting billet on the appropriate machine to ensure maximum efficiency on production.
A high- quality and efficient lubrication system is yet another way to significantly reduce cost. Equal and adequate lubrication is key during cold forging, especially products that need multiple station presses. By implementing this system, failures or flawed products can be greatly reduced thanks to the coating of lube, which decreases the chance of having to re-forging a batch of items, and ultimately, minimizing unnecessary cost.
Specification
Material 6061-t6 strength HB>95 surface red anodic oxidation for Great Wall harvard auto parts auto shock absorbers
surface treatment | anodizing |
technics | Aluminium alloy forging |
application | auto spare parts |
sample | free 2 |
certification | ISO;TS |
oem | accept |
capacity | 0.5k |
color | red |
aluminium alloy forged parts supplier,5052P-H32 ,2A12,2A14,5052,7A04,2A11,2014,2024,7A09,5A05,7075 T6 precision hot/cold forging process,CNC machining, anodizing surface treatment
aluminum part forgings + precision CNC machining + Surface treatment,one-stop services.
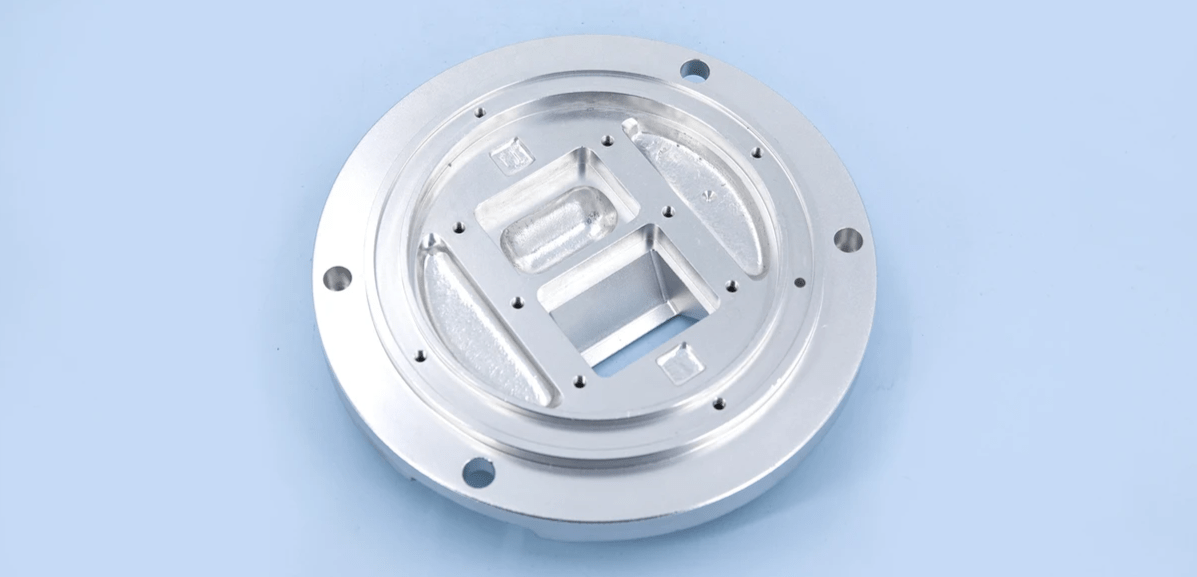
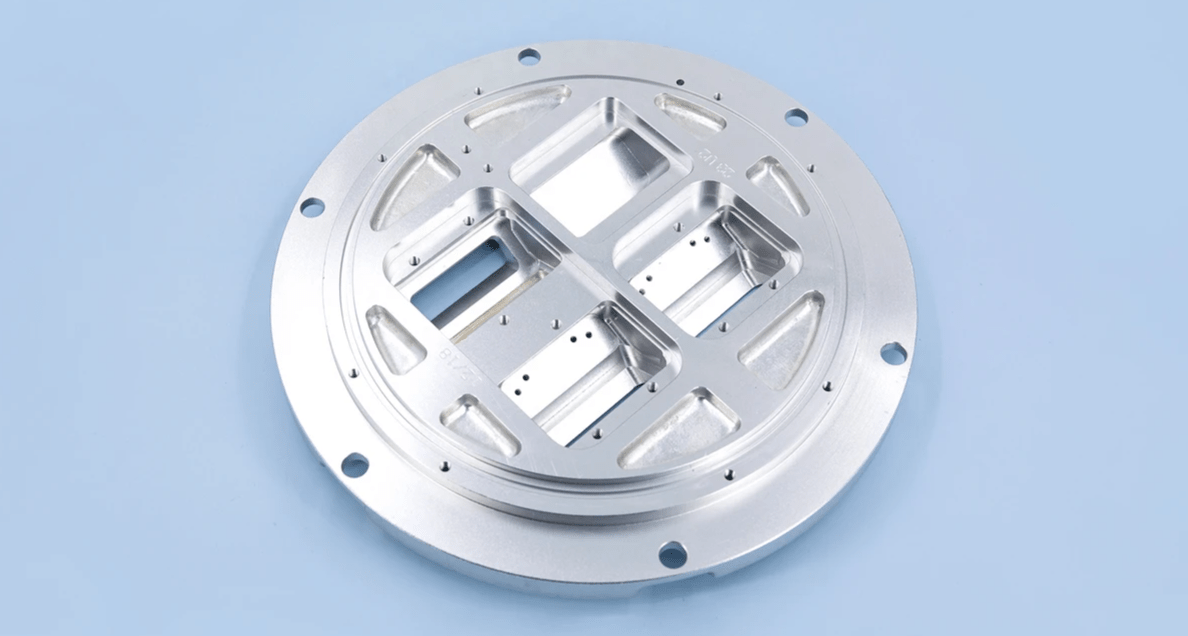
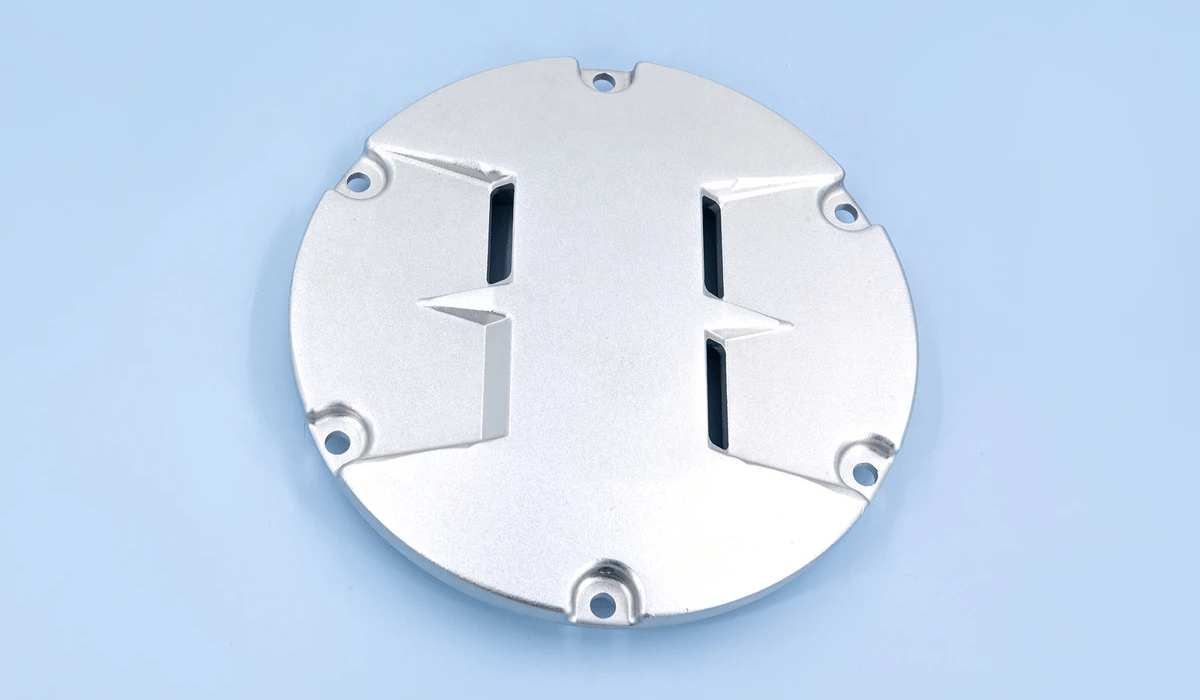
ISO TS 16949 aluminum forging enterprise, forging components, aluminum alloy heat treatment, anodizing Aluminum forging services
Aluminium Forging Industrial Hardware Components,
Aluminum Forging Vehicle Parts,
Aluminum Forging Bicycle/BIKE Parts,
Aluminum Forging Motorcycle Part,
Aluminum Forging Automobile Parts,
forged aluminum manufacturer,Aluminum alloy forgings supplier,brass aluminum forge enterprises, 6082 7075 t6,anodized aluminum forging companies, ISO TS 16949,IATF16949
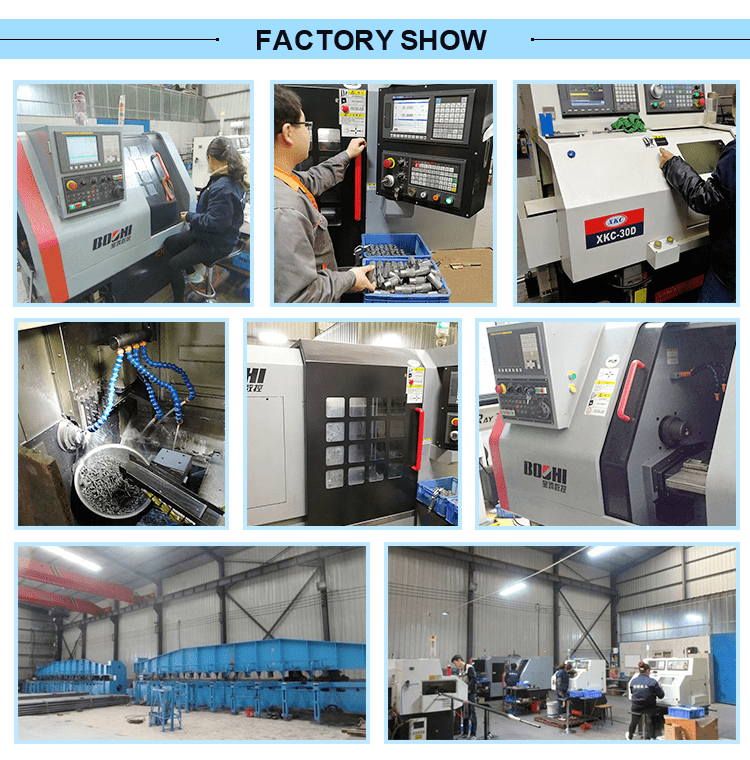
factory had the precision forging presses and lines for kinds of aluminum parts, round, square, long square or with other shapes.
The aluminum forging parts mainly used in below fields:
1. Avition and aircraft. The aluminum forgings on the aircraft account for about 70% of the weight of aircraft materials, such as landing gear, frame, rib, engine parts, moving ring and fixed ring. There are thousands of forgings used on an aircraft, and most of them have been aluminized, except a few high-temperature parts use high-temperature alloy and titanium alloy forgings.
2. Weapon industry. The number of aluminum alloy forgings used as load-bearing parts on conventional weapons such as tanks, armored vehicles, personnel carriers, combat vehicles, rockets, gun racks, warships and so on has greatly increased, basically replacing steel forgings. In particular, aluminum alloy tank load wheels and other important forgings have become important materials for lightweight and modern weapons and equipment.
3. Vehicles. Automobile is the most promising industry using aluminum alloy forgings, and also the largest user of aluminum forgings. It is mainly used as wheel hub (especially for heavy vehicles and large and medium-sized buses), bumper, base beam and other small aluminum forgings, among which aluminum wheel hub is the aluminum forging with the largest usage, mainly used on large buses, trucks and heavy vehicles.
4. Energy and power industry. Aluminum forgings will gradually replace some steel forgings to make frames, retaining rings, moving rings and fixed rings, as well as coal transport wheels, which are generally large and medium-sized forgings.
5. Transportation machinery and railway locomotive industry. Aluminum alloy forgings are widely used as cylinders, piston skirts, connecting rods, etc.
6. Mold industry. Aluminum alloy forgings are used to make rubber molds, shoe molds and other light industry molds.
7. Electronic communications, household appliances, sports equipment. Aluminum forgings have also been used to replace steel and copper forgings.
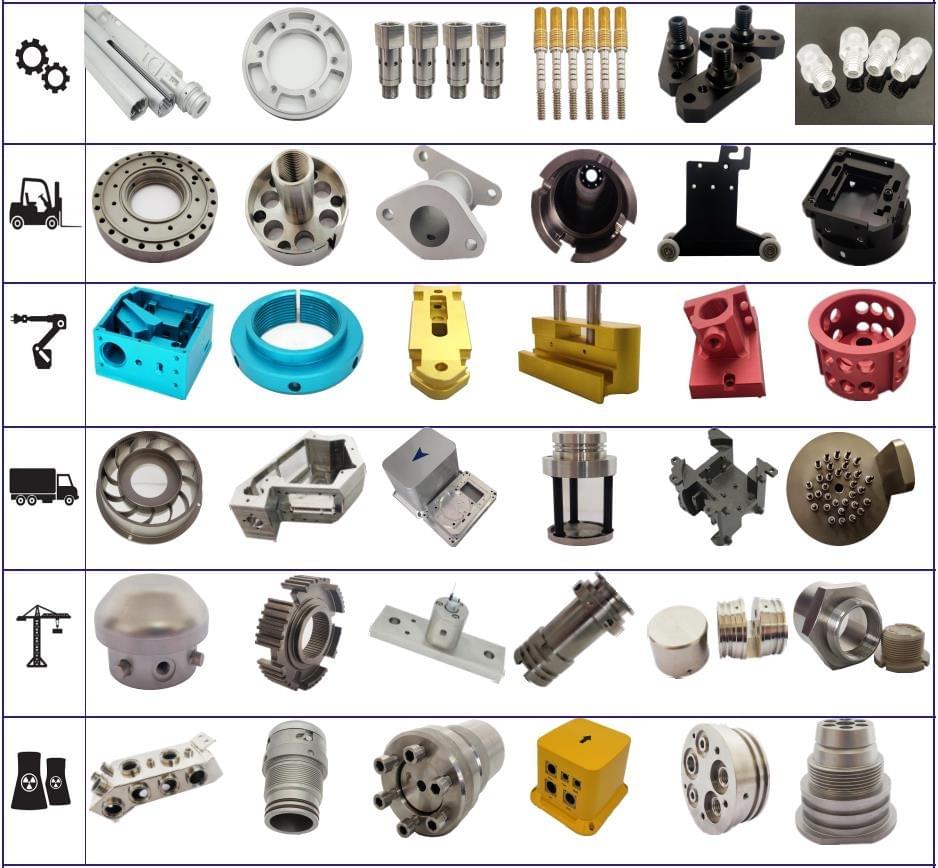
Process | Aluminum Die casting, Squeeze casting+T6, Zinc Alloy die casting,CNC machining, Turning |
Equipment | Cold chamber die casting machine:200T/280T/400T/600T/800T/1100T.CNC centers, CNC turning, CNC lathes, electrical pulse, line cutting, milling, drilling, grinding |
Material | A319, A356, A360, A369, A380, A383, A384, A413, A535, 44300, 44300, 46000, AlSi9Mg, AlSi9Cu3, ADC12, ZL102, ZL104, ZL108, Zamak2,3,5,7 ect. Squeeze Casting: A356+T6, A356.2+T6, AlSi9Mg+T6, Zl108+T6, AlTi-Alloy+T6 |
Surface | Trimming, Deburring,Polishing, Shot blasting, Sand blasting,Tumbling, Powder coating, Anodizing, Chrome, Zinc, Electrophoresis, Passivation, Chemical coating. |
Software Assistance | Pro-e/Solid work/UG/Auto CAD/CATIA |
Products Application | Automotive industry, Bicycle and motorcycle, Door and windows and furniture, Household appliance, Gas meter, Power tool,LED lighting, Medical instrument parts, ect. |
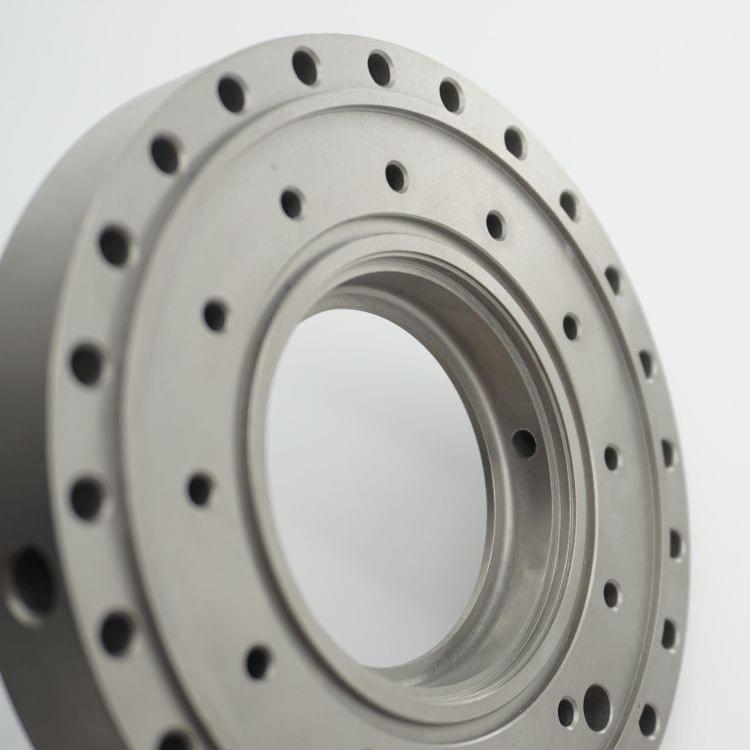
2014 is a precipitation hardened alloy. Its forgings achieve a high level of strength after heat treatment and are used in the frame structure of trucks and aircraft.
6061 is one of the most common aluminum alloys and is capable of being hot forged into a variety of automotive, marine, and structural components.
7050 is a heat treatable aluminum alloy. With good resistance to stress corrosion cracking, 7050 aluminum forgings have good mechanical properties such as toughness and strength.
7075 exhibits high levels of strength as well as good mechanical properties at lower temperatures. 7075 aluminum forgings are commonly used for aerospace and air craft structures.
7079 has a yield strength that is higher than those of most other aluminum alloys. 7079 aluminum forgings exhibit good mechanical properties and are often used in structural applications where light weight is critical.
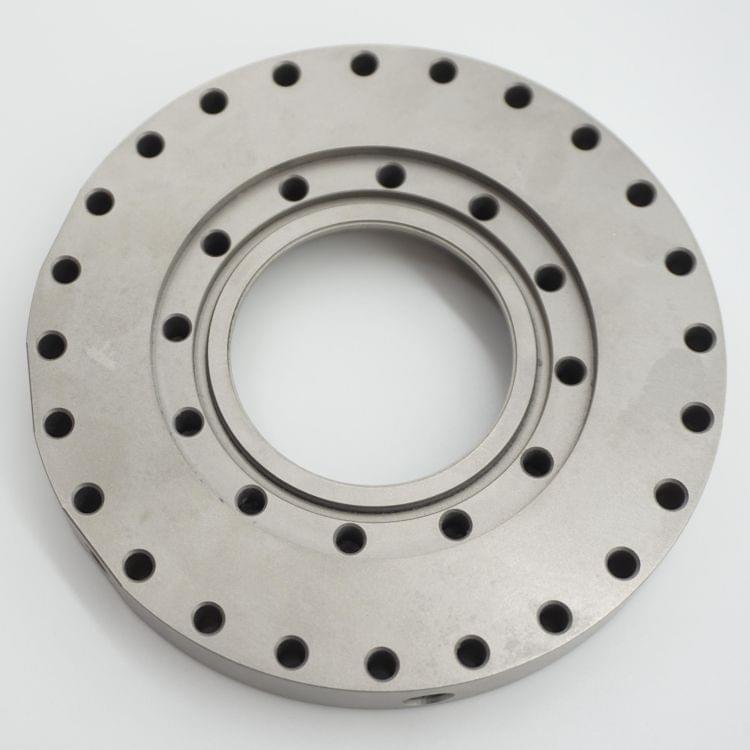
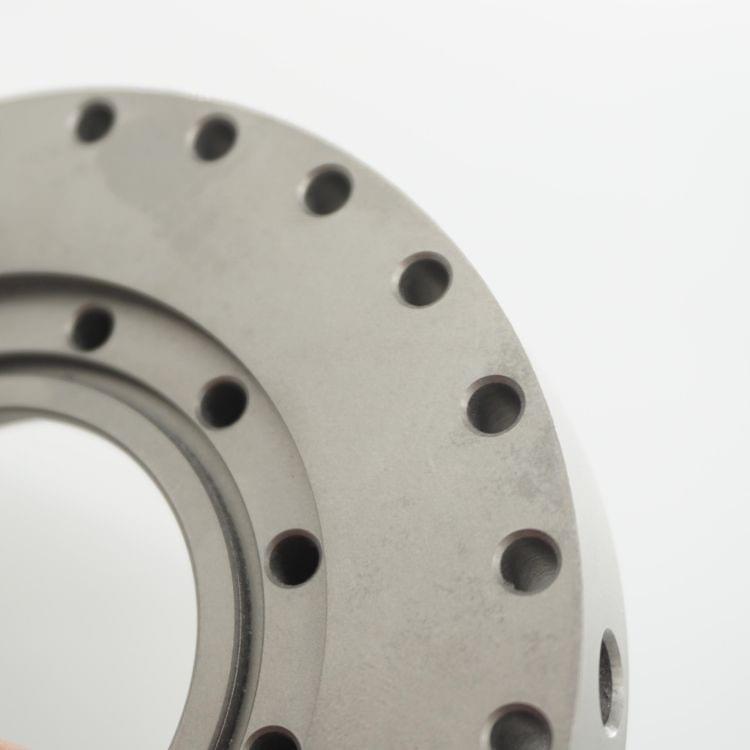
Artisan industry trading (Nantong) CO.,LTD professional in ADC12 /Al-Si-Cu Aluminum alloy die-casting production, aluminum alloy high-strength squeeze die casting(Auto Parts Squeeze Casting Parts), plastic injection production, and mold R&D and manufacturing.
Focus on the development of technical services for lightweight equipment, processes and products. We have successfully provided a complete set of solutions in light alloy precision forming for hundreds of domestic and oversea customers, helping customers solve many production technical problems and achieve value increasement, the industries include automobiles and motorcycles, communications, engineering machinery, aviation, and electronics etc.
What's important, our factory have below advantages:
--10 Years Aluminum Die casting/ forging Experience .
--One-stop service :Drawings--Mold development--Casting production--Surface treatment.
--Manufacture factory with Competitive price , Higher quality .
--Leading domestic aluminum alloy squeeze casting technology
Artisan industry trading (Nantong) CO.,LTD
ADD: No.13 ZhouZhuang Community, JiangAnTown, RUGAO city, JIANGSU CHINA
TEL/WhatsUP: +86 150 5061 5346
https://www.artisanmake.com
Email:info@artisanmake.com
lilychin@vip.163.com
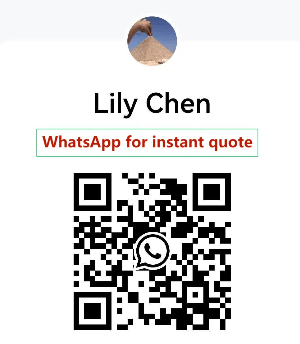