6A02 forging aluminum is an aluminum alloy, which is mainly used for manufacturing aviation equipment, daily life supplies, buildings and windows for buildings.
Material name: Transformer aluminum and aluminum alloy
Plate: 6A02
Features and applications:
6A02 aluminum alloy, US deformation aluminum and aluminum alloy. Aluminum alloy is divided into two categories: cast aluminum alloy and use in cast state; deformation aluminum alloy can withstand pressure processing, and the mechanical properties are higher than the casting state. Can be processed into aluminum alloy materials with various forms and specifications.
Standard comparison:
American Aluminum Association (AA) 6003, UNSA96003, isor209ALMG1SI
chemical composition:
Aluminum Al (minimum value): balance
Silicon, SI: 0.35 ~ 1.0
Iron, Fe: ≤0.6
Copper, CU: ≤0.10
Manganese, mn: ≤0.8
Magnesium, mg: 0.8 ~ 1.5
Chromium, CR: ≤0.35
Zinc, zn: ≤0.20
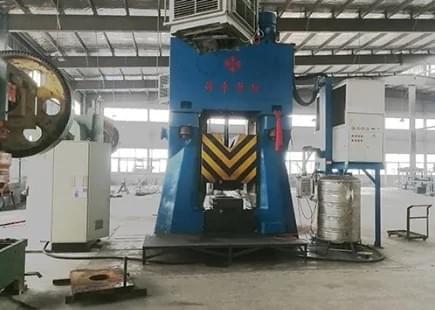
What is aluminum forging?
Aluminum forging is one of the two major components of the two major components that use the forging machine to apply the aluminum blank to the two major parts of the two major components of the processing method of a certain mechanical performance, a certain shape and dimensional forging, and forging (forging and stamping).
By forging, the lava loosening and other defects that can be eliminated during the smelting process optimize the micro -tissue structure. At the same time, due to the preservation of a complete metal streamline, the mechanical properties of the forging parts are generally better than the castings of the same material.
Casting generally uses a vertical or horizontal water -cooled semi -continuous casting method. In order to improve the tissue and surface quality of the vertical casting, the electromagnetic crystal groove, the short crystal groove and the hot top casting method have also been developed (see the solidification of the metal).
The water -cooled semi -continuous casting method is to introduce liquid metal into the crystallizer used in water cooling through a stream tank, so that liquid metal cooling to form a solid shell, which is trapped by the foundation of the castor or a uniform weight of its own weight.
The process parameters are very different due to the difference in the size of the alloy and the size of the ingots. Generally, the casting speed and cooling speed should be increased as much as possible to reduce the height of the crystal groove. The casting temperature is usually 50-110 ° C higher than the liquid line of alloy. In addition, the continuous casting process of aluminum plate belt has been developed.
What is the difference between aluminum and forged aluminum?
The basic difference between forged aluminum and cast aluminum is that the aluminum forging process does not melt the work piece material to create a new shape.
Is forged aluminum stronger?
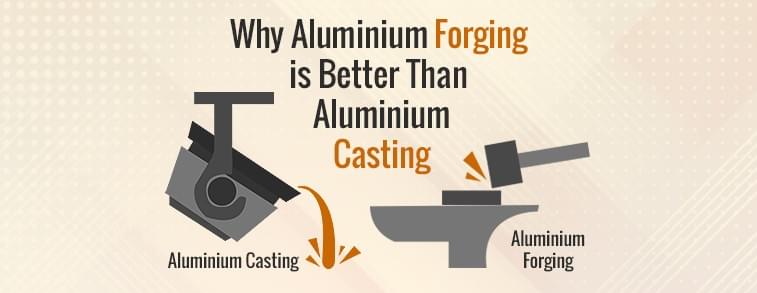
Unlike the latter, forging is porosity-free. Which means, it allows heat treatment processes that vastly augment the selected mechanical characteristics. This greater strength goes on to show that aluminum forging can attain good strength unlike other methods.
Is forged aluminum stronger than steel?
Weight Differences between aluminum and steel
Even with the possibility of corrosion, steel forging is harder than aluminum forging due to the different desities of steel and aluminum. Steel forging is strong and less likely to warp, deform or bend under weight, force or heat.
Is forged aluminum alloy stronger than cast?
Due to its tighter grain structure, forged wheels are also mechanically stronger, ensuring better wear resistance over time. You also get better performance and handling because of this process. The cast wheel manufacturing process involves heating up aluminum until it reaches a molten state.
How can you tell if its a cast or forged?
When something is cast, the material is heated above its melting temperature and poured into a mold where it solidifies. When something is forged it is physically forced into shape while remaining in a solid state – although it is frequently heated.
Is forged better than cast aluminum?
Forged steel is generally stronger and more reliable than castings and plate steel due to the fact that the grain flows of the steel are altered, conforming to the shape of the part. The advantages of forging include: Generally tougher than alternatives.
Forged parts had a 26% higher tensile strength than the same cast parts. Forged parts had a 37% higher fatigue strength resulting in a much longer lifespan than cast parts.
What is better forged or billet aluminum?
Metallurgists agree that a forged piece of aluminum is stronger than cast or billet. The reason being, when the material is shaped under pressure, its 'grain' follows the same shape as the part. As a result, the product manufactured is stronger due to the continuous grain characteristics allowed by the forging process.
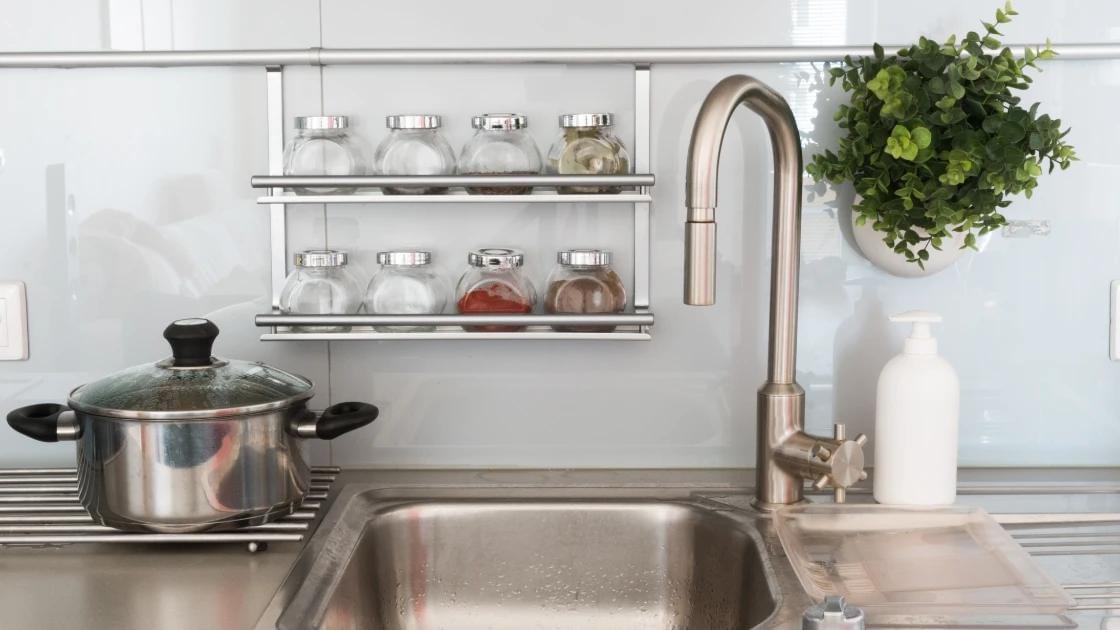
Is aluminium better than stainless steel?
When comparing stainless steel vs aluminum, stainless steel has much better resistance to heat with a melting point of 2500 ℉, while aluminum becomes very soft around 400 ℉ with a melting point of 1220 ℉. However, aluminum has the advantage over steel in cold temperatures
How is forged aluminum made?
“Forging is a manufacturing process where metal is pressed, pounded or squeezed under great pressure to produce high-strength parts. Forged aluminum is ideal for applications where performance and safety are critical but a lighter-weight metal is needed for speed or energy efficiency.
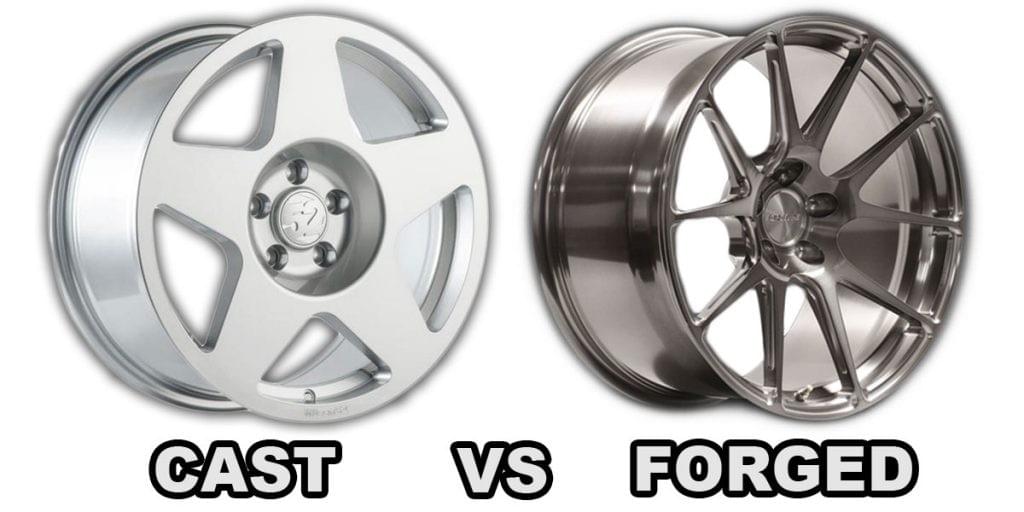
What is the difference between Forged Aluminum versus Cast Aluminum ?
There are differences between forged vs cast material. The basic difference between forging and casting is that the forging process does not melt the work piece material to create a new shape. In casting, metal is melted and poured or forced into a mold made in the shape of the desired item. In forging, deformation of the material in solid form, often by hammering or pressing the material, creates the desired shape. Both processes have certain advantages that may lead to one or the other being used to create a component depending upon cost and service use requirements. Aluminum and aluminum alloys are subject to the same metallurgical principles as other metals which will determine which process provides the advantage for a given end-use item.
Cast Aluminum
When metal is melted and casting is produced, a product of complex shape can result, only limited by the mold making and the flow and solidification dynamics of the metal. This allows casting to economically produce components with internal chambers and external features that reduce the number of subsequent metal removal operations performed to complete a finished part. The disadvantage is the potential for contamination while metal is in a liquid state from impurities entering into the liquid. Formed while ingots and additives are being melted, impurities may not be sufficiently filtered from the liquid metal as it flows into the mold. Small pieces of the conduits leading to the mold or the mold itself can also flake or break, entering the liquid. Turbulence as liquid metal flows through complex chambers may result in voids and internal, hidden, areas of non-fill. Alloy segregation while the metal is in liquid form can result in inconsistent material properties from one area of the casting to another. Defects such as tears or cracks can form when different sections mass cools at different rates as the metal solidifies.
Forged Aluminum
Forging has the advantage of the addition of deformation energy to further refine and improve the metallurgy of the shape being created. Through mechanical and thermomechanical deformation energy applied, originally cast ingots of aluminum are shaped and reshaped, changing the internal microstructure. Any inclusions or alloy concentrations are dispersed, and any voids are crushed and eliminated. Forging energy drives the recrystallization of the microstructure, creating enhanced durability and toughness. Forgings are not usually able to produce shapes as complex as castings. This often requires additional finishing operations which adds to the cost of using forgings, compared to castings. The improved properties of forged product outweigh cost issues, however, when safety, reliability and the cost of component failure are the greatest challenges.
Forged Aluminum
Forging Aluminum into Alloys
An additional advantage of forging is the ability to form and shape alloys consolidated from metal and other additive powders. Alloys and matrix materials of this type are produced and consolidated as powders as the constituent elements cannot be successfully melted and cast. Thermomechanical energy is often the most practical means to consolidate powders into solid form. Deformation processes such as forging are then used to further shape these materials, in a solid state, to more useful, near net forms, providing improved economy for use of these more expensive materials. In this way, forging is ensuring the capability and usability of materials that provide properties that will meet future design challenges.
Forged products will be the choice when components must exhibit maximum properties and durability in service, where weight and mass must be minimized and failure would be costly or catastrophic. Other processes seek to claim “wrought properties” but only the forging process can consistently and reliably supply it.
the difference between Aluminum alloy open die forging vs closed die forging?
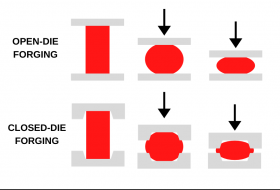
Open die forging is the process of deforming a piece of metal between multiple dies that do not completely enclose the material. The metal is altered as the dies “hammer” or “stamp” the material through a series of movements until the desired shape is achieved.
Closed Die Forging is a forging process in which dies move towards each other and covers the workpiece in whole or in part. The heated raw material, which is approximately the shape or size of the final forged part, is placed in the bottom die.
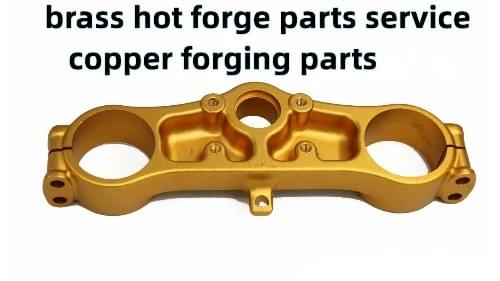
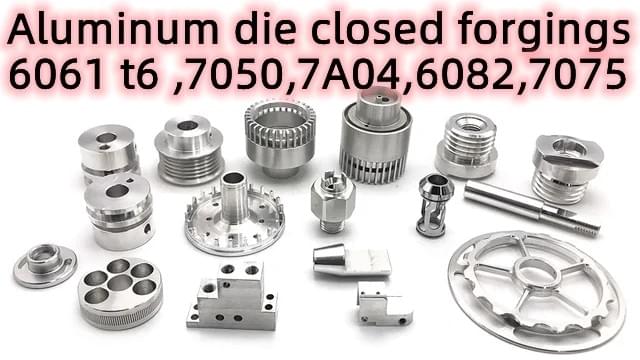
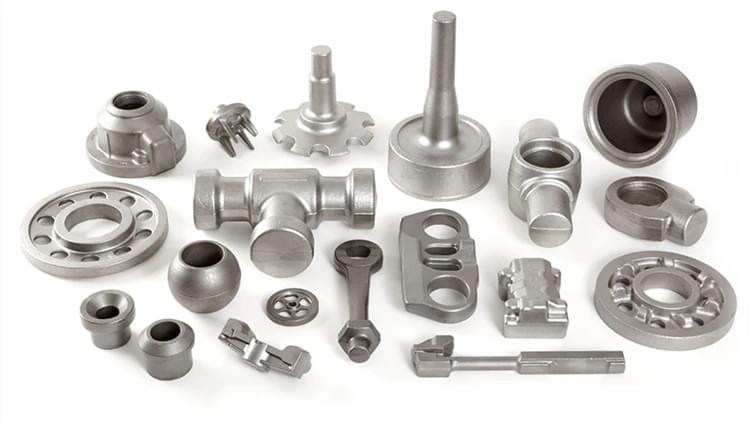
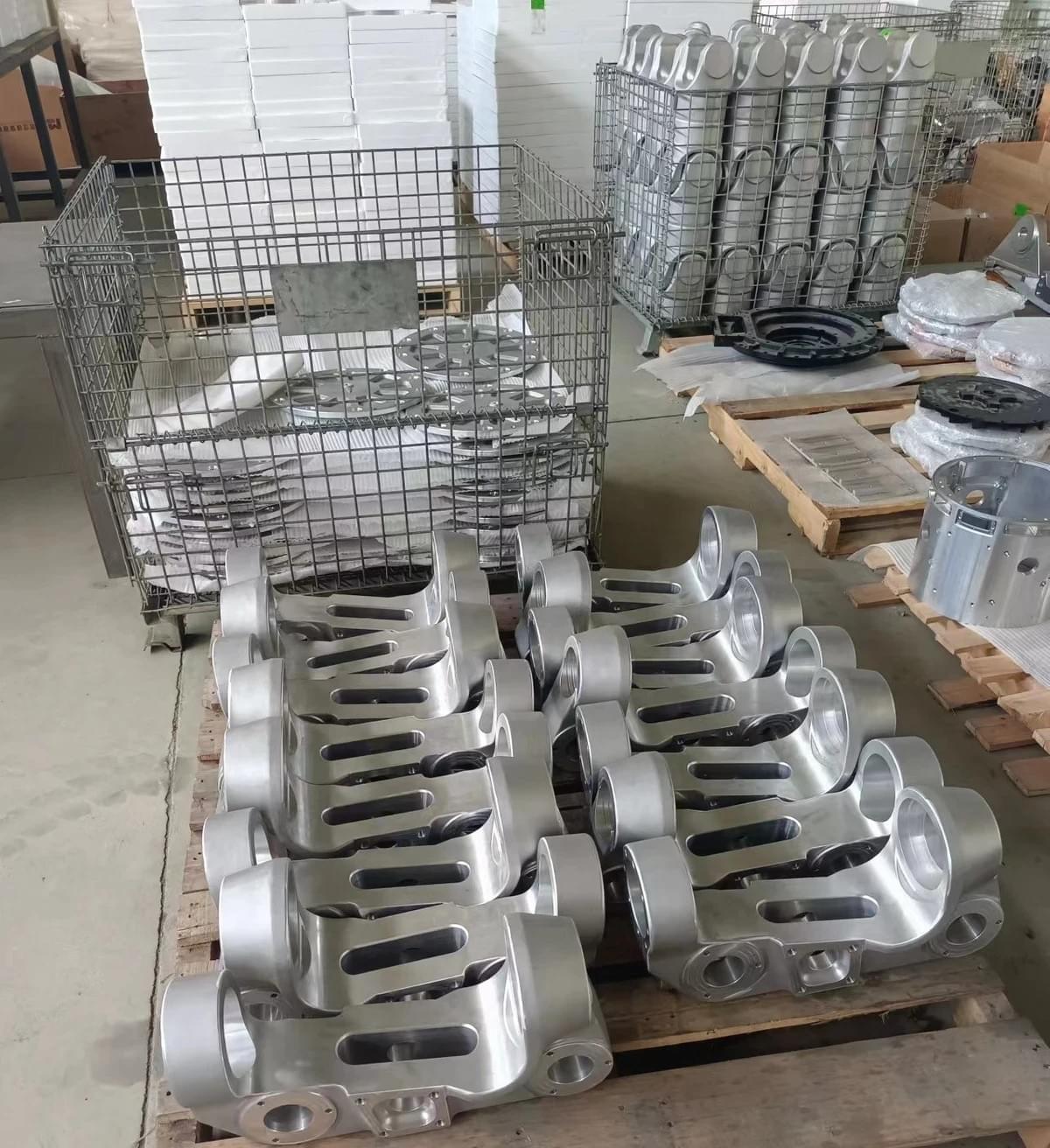
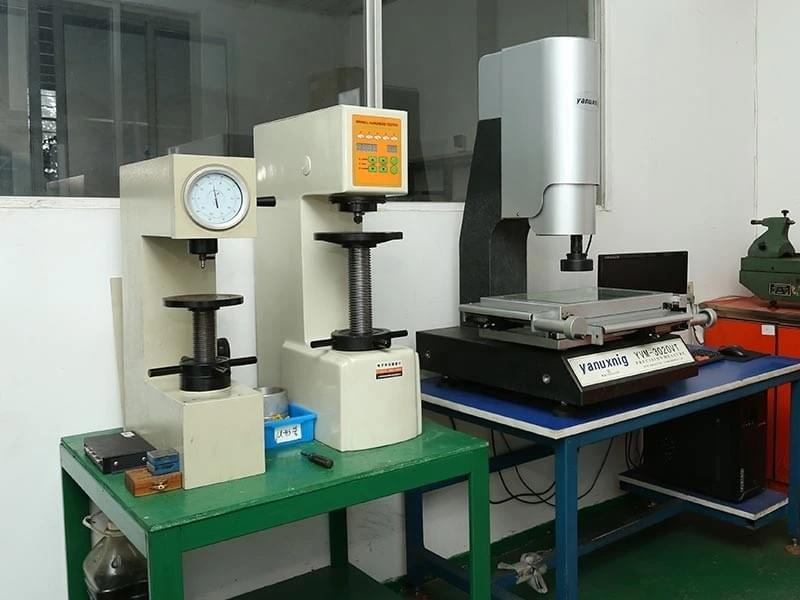
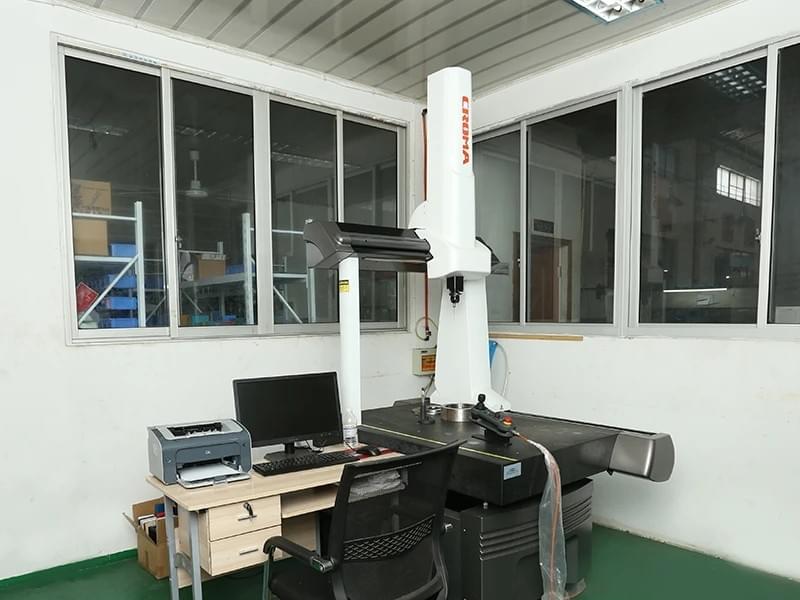
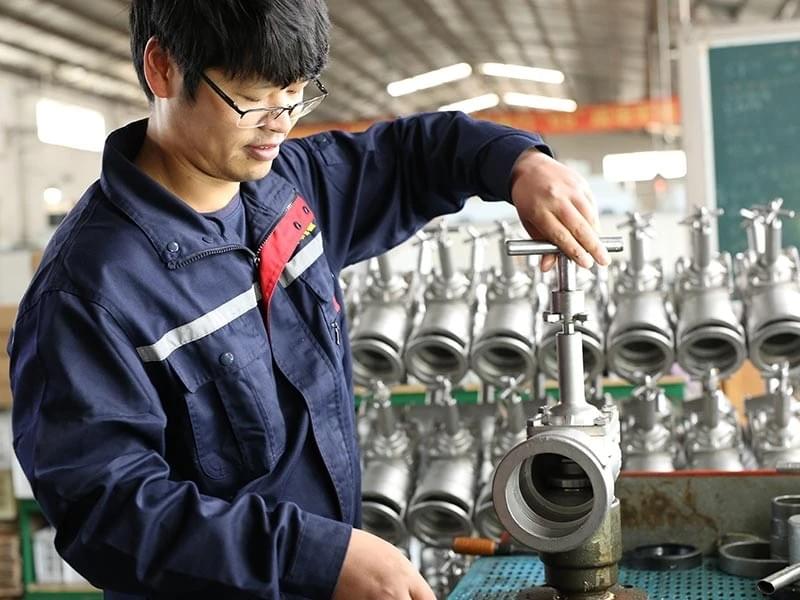
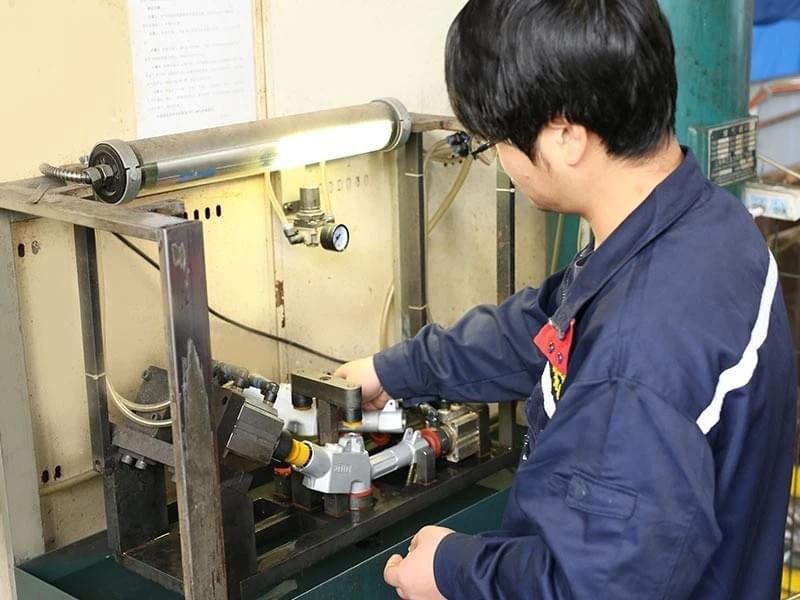
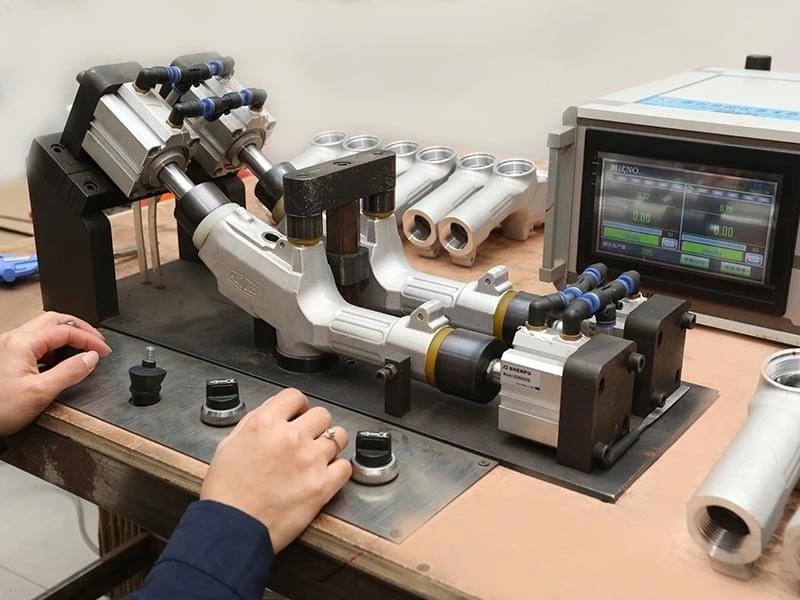
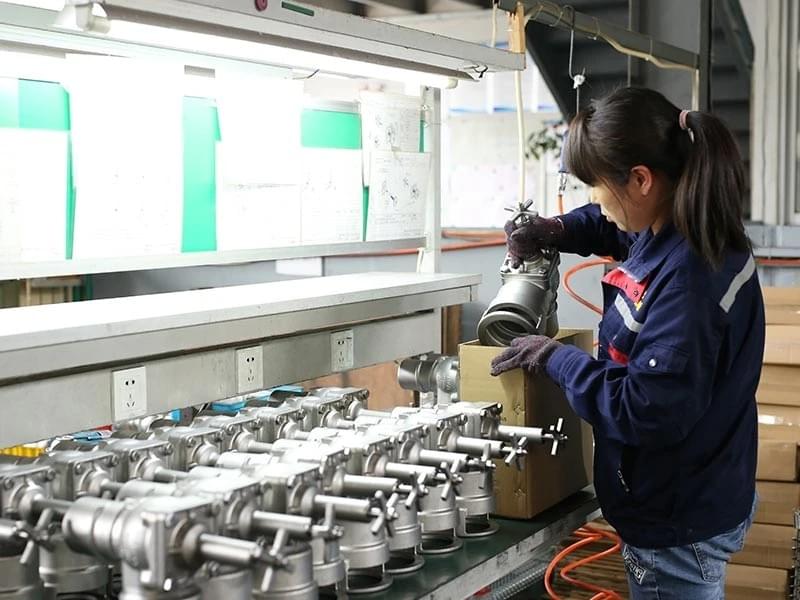
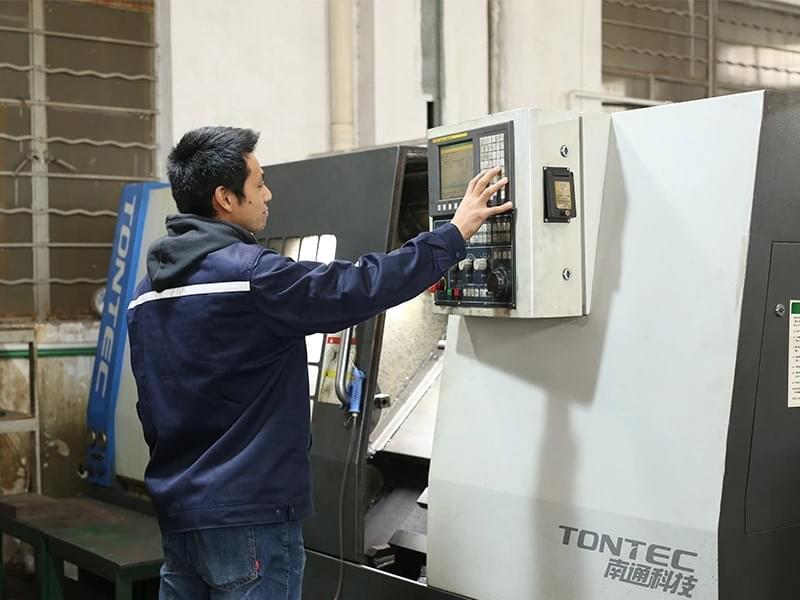
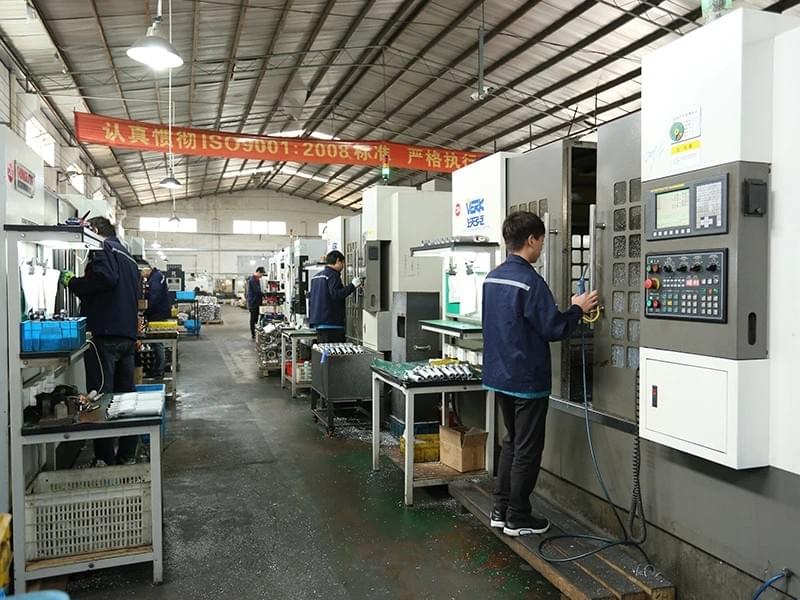
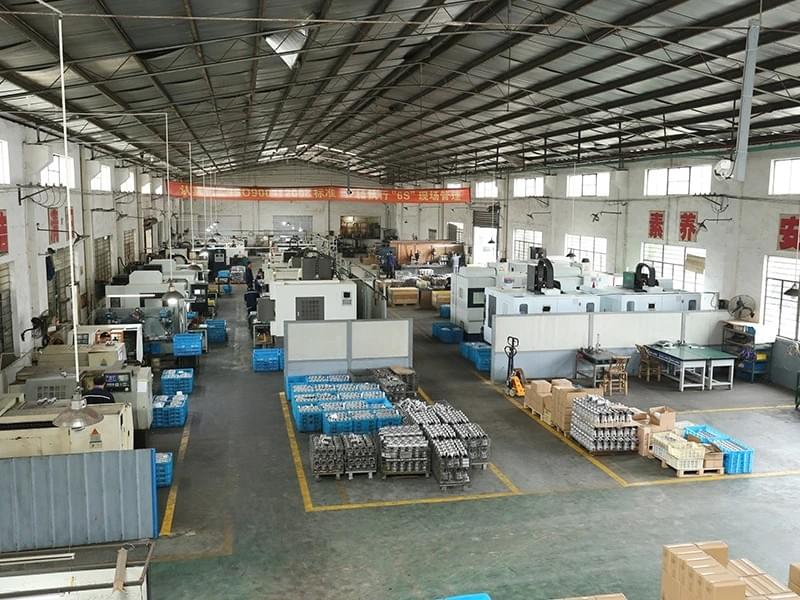
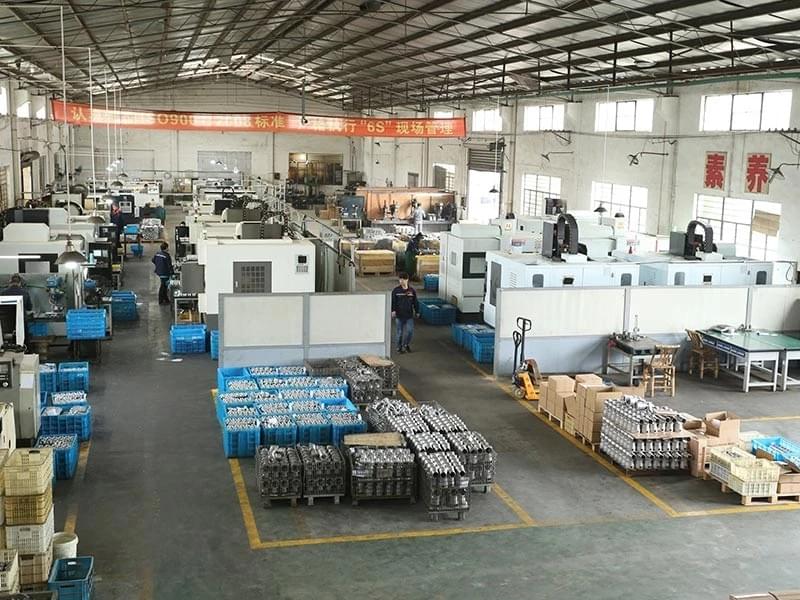
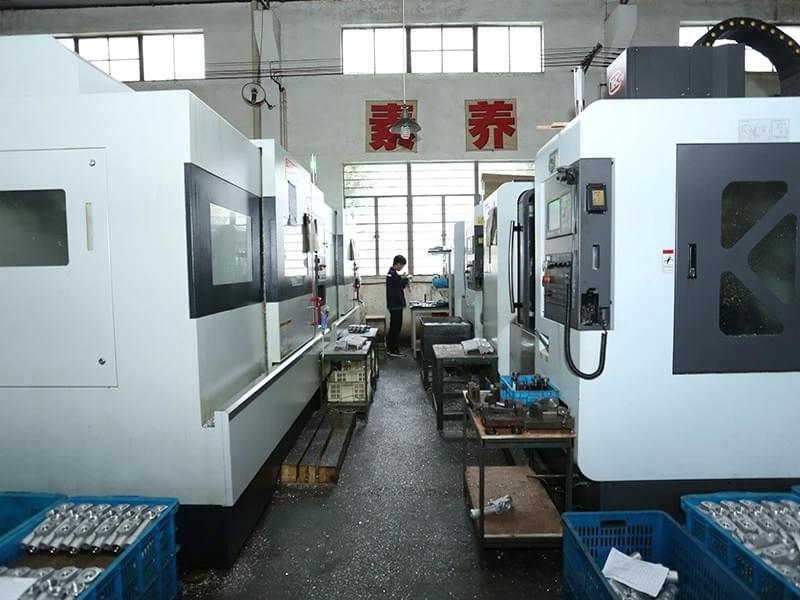
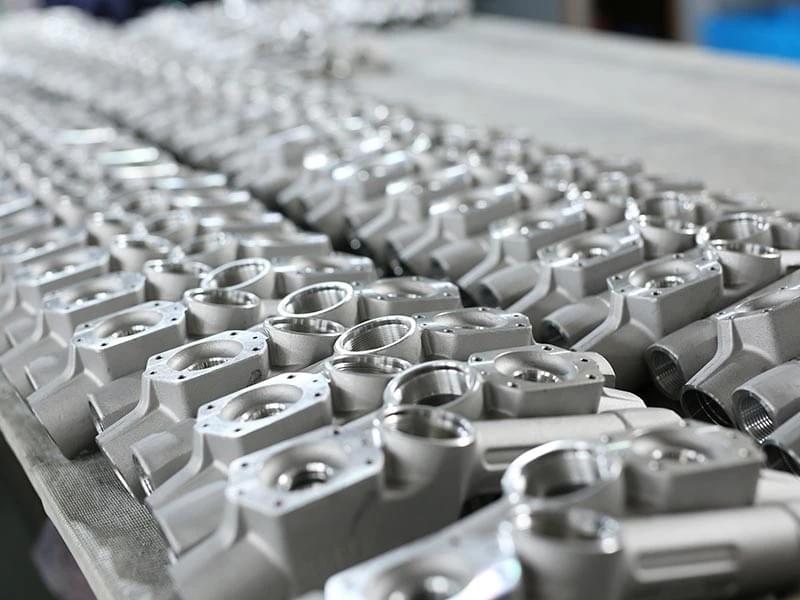
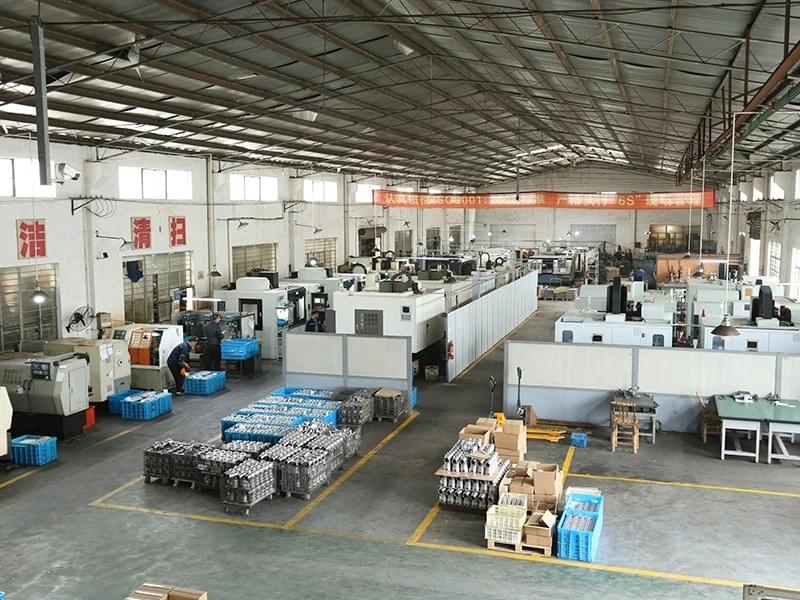
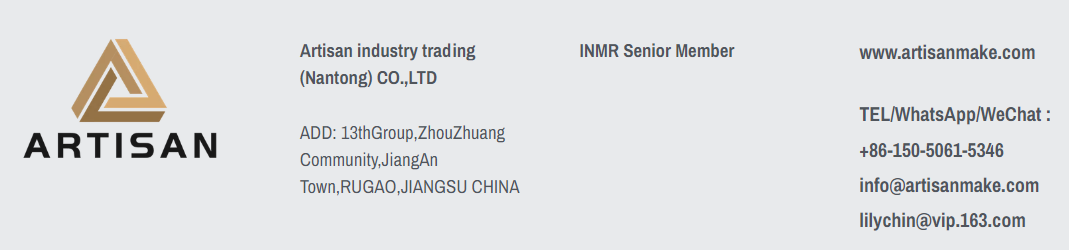