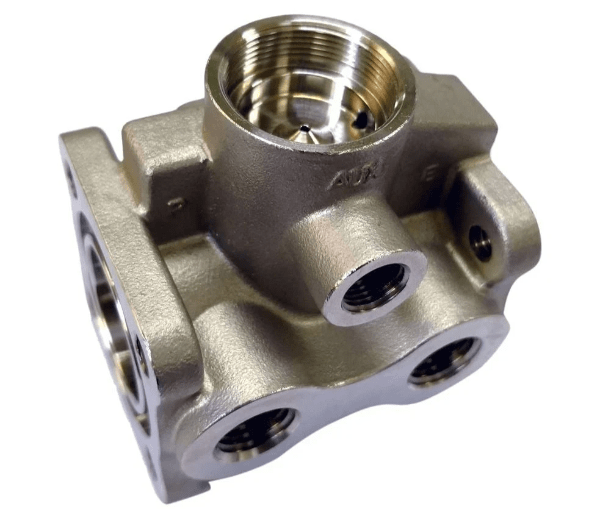
There have two types of investment cast processes for stainless Casting:Silica Sol process and the water glass process.
The Silica Sol process is used to cast complex high quality parts with requirements of a very good surface finish and close dimensional tolerances.
The water glass process is typical of the process in the early stages of investment castings. It generally is capable of much larger castings than the Silica Sol process, but does not have as good of surface finish or tolerances. The water glass process provides parts that have better surface finish and dimensional tolerances than sand castings.
Silica Sol investment cast parts can range from a weight of just a few ounces to approximately 80 pounds. If you are concerned with precision in very small parts, we are especially proficient at very fine detail work including teeth and serrations. Water glass castings may range in weight from several ounces to approximately 200 pounds.
First article layouts and spectrometer material certifications are provided with all first article samples.
A variety of secondary operations can be performed on both types of investment castings. They include heat treatment, machining, plating, painting, polishing and buffing, assembly services and even custom packaging.
Please check below for whole production process:
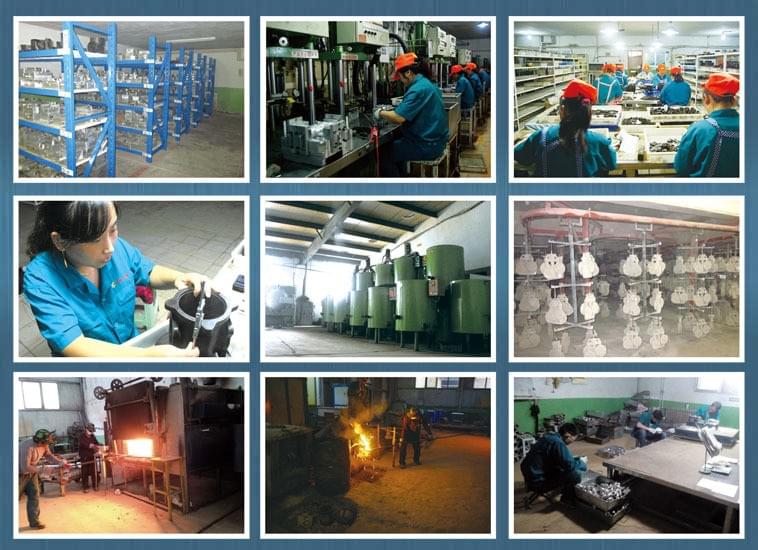
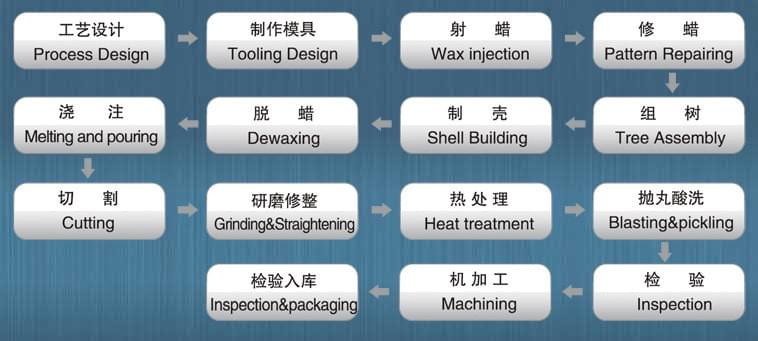
stainless Sand casting is perhaps the oldest and most commonly used type of metal forming in the marketplace today. It is capable of forming both large and small parts and can be used for a number of different materials.
We have green sand castings, resin sand casings and water glass sand castings in both ferrous and non-ferrous materials.
Perhaps the most common green sand castings would be made from either grey iron or ductile iron. We can supply these castings from approximately 0.05Kg to approximately 15000 Kg and up to 5000mm x 2000mm x 1500mm in size for the largest part. Molding methods range from floor hand molding, jolt squeezer lines and automatic molding lines. With this variety of molding methods we are able to accommodate the weight, size and quantity the customer requires.
Steel sand castings are available both as water glass sand castings and resin sand castings, and are available in plain carbon, alloy and stainless steels. In the category of steel sand castings the smallest available part would be approximately 1Kg while the largest would be approximately 20 tons. Steel castings smaller than the 1Kg range would be made from investment casting(lost wax casting) method.
Non-ferrous sand castings are also available. The molding process used is green sand and we can accommodate requests for castings weighing from 0.1 Kg to 100 Kg. The alloys that are available include copper base and aluminum base alloys.
First article layouts and spectrometer material certifications are provided with all first article samples. Specialized inspection reports can be done per customer request.
A variety of secondary operations can be performed on all three types of sand castings. They include shot blasting, heat treatment, machining, surface treatment, assembly services and even custom packaging.
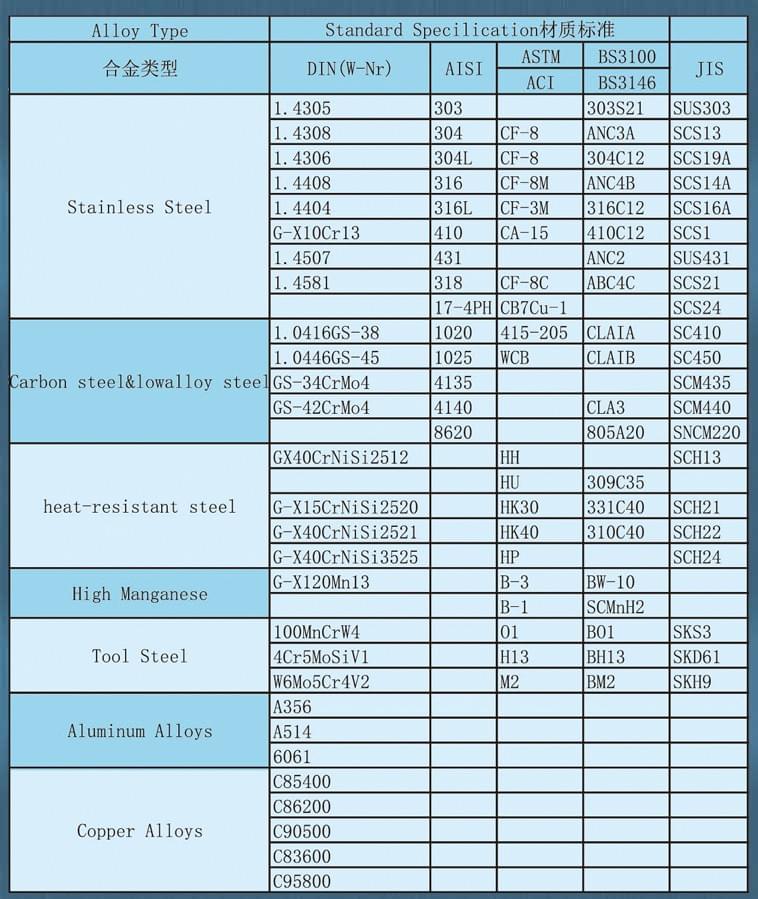
Stainless Die casting is the process where molten metal is injected into a mold under high pressure in the range of 10 to 210 Mpa. This will result in a highly uniform casting with very good surface finish and exceptional dimensional accuracy. Usually this can either eliminate or greatly reduce the machining required to finish the part. We could offer both the cold chamber process and the hot chamber process. In the cold chamber process the metal is ladled into the injection chamber for each shot. This is less exposure of the molten metal to the chamber walls and plunger. This is very useful for aluminum and cooper alloys that would easily alloy with iron at elevated temperatures. The hot chamber process has the injection chamber which is connected to the die cavity permanently immersed in the molten metal. The hot chamber process is used for metals of low melting point and high fluidity such as tin and zinc. Minimum wall thickness and draft angles for the die castings are as follows:
Die casting material including alloys of aluminum, copper, zinc and magnesium. Zinc castings can be made with thinner wall thickness than aluminum due to high melt fluidity. our factory produce parts from very samll to about 30Kg for aluminum, 10Kg for magnesium, 50Kg for zinc and 5Kg for copper.
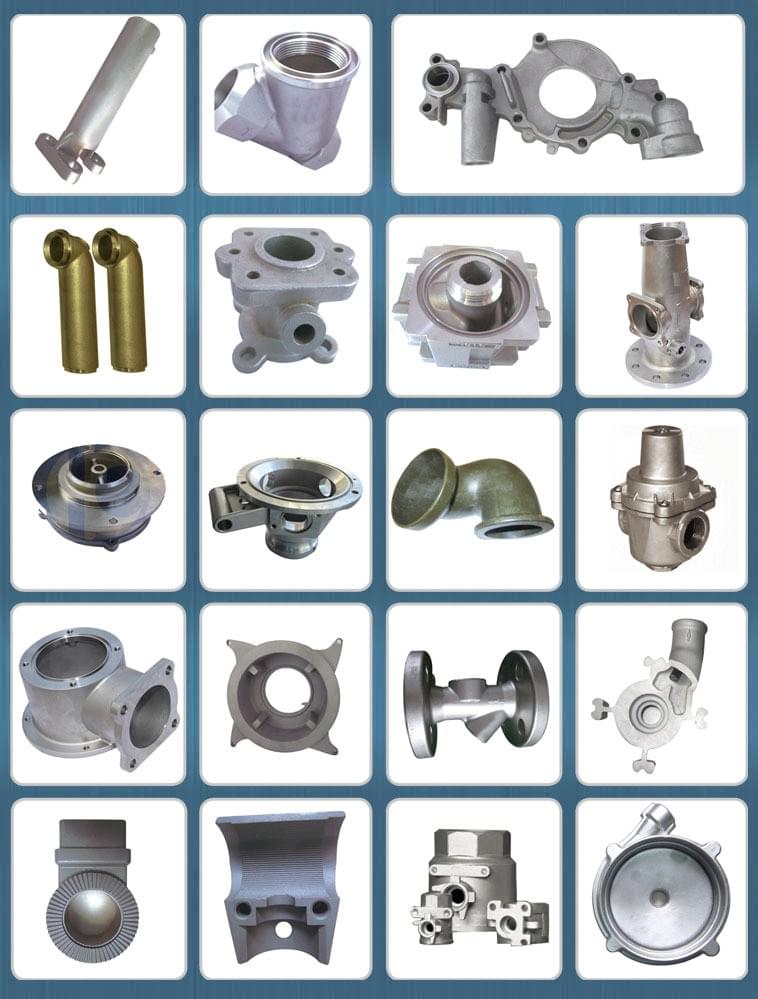
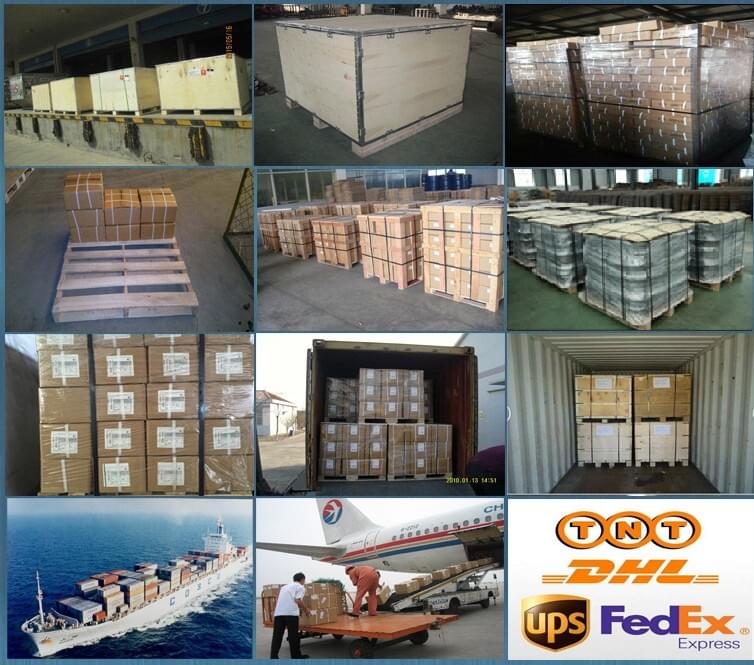