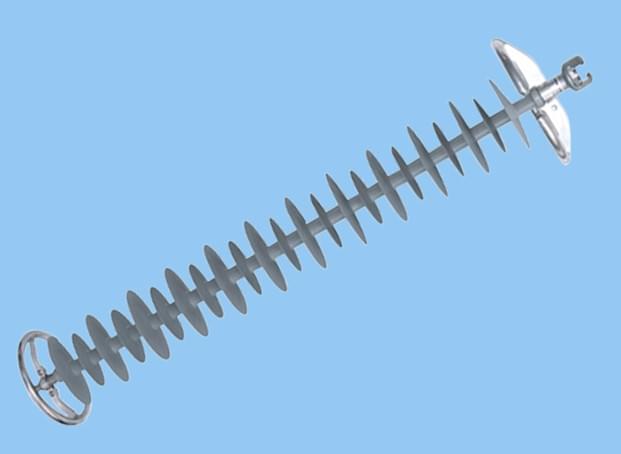
1. Introduction of composite long rod polymer insulators
Artisan Industry is professional Composite long rod polymer insulators manufacturer in China.
2. Technical standards for insulators
The composite insulators designed, manufactured and tested according to IEC 61109 standard, with end-fittings according to IEC 61466-1, galvanized metal ends, and also many other standards as below:
American national standards institute
- ANSI C29.11 Tests for composite suspension insulators for overhead transmission lines
- ANSI C29.12 Composites suspension types
- ANSI/IEEE 4 Techniques for high-voltage testing
American society for testing and materials
- ASTM A153 Zinc coating (hot-dip) on iron and steel hardware
- ASTM A239 Test method for locating the thinnest spot in a zinc (galvanized) coating on iron or steel articles by the Preece test (copper sulfate dip)
International electrotechnical commission
- IEC60060-2 High voltage test techniques
- IEC61109 Insulators for overhead lines - Composite suspension and tension insulators for ac systems with a nominal voltage greater than 1 000 V - Definitions, test methods and acceptance criteria •IEC61109 - Amendment 1
- IEC60587 Electrical insulating materials used under severe ambient conditions – Test methods for evaluating resistance to tracking and erosion
- IEC61466-1 Composite string insulator units for overhead lines with a nominal voltage greater than 1000 V - Part 1: Standard strength classes and end fittings
- IEC61284 Overhead lines - Requirements and tests for fittings
- IEC60437 Radio interference test on high-voltage insulators
- IEC 36-Sec. 71 Tests of composite insulators for ac overhead lines with a nominal voltage greater than 1000 V
3. Physical characteristics of the insulators
Composite insulators have characteristics and composition similar to those established in clause 3 of standard IEC-61109. The raw material for the insulation material (cover and core and fins) is 100% silicone rubber polymer (Silicon Rubber) before the process of adding additives. The finished product will not contain more than 20% carbon by weight. Usually the long rod polymer insulators are made of polymer housing, ECR fiber glass rod, metal end fittings, corona rings etc.
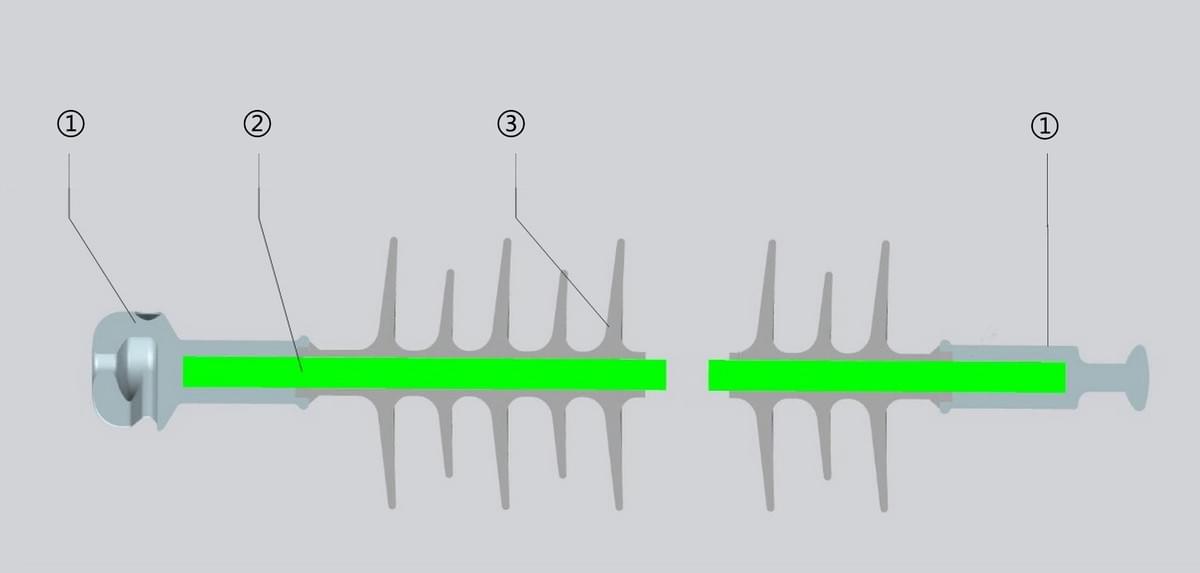
1- End-fittings 2- Core 3- Housing
3.1 Housing (sheath and sheds)
The sheath are made of HTV-type silicone rubber, which protects the core against ultraviolet light and attacks from external agents, ensuring watertightness and
good behavior in polluted environments. The types of rubber to be used are completely free of ethylene-propylene-diene monomer (EPDM). The silicone rubber must be protected
against high temperatures produced by partial discharges, electric arcs and tracking on the insulator, for which Alumina Trihydrate (ATH) with a particle size between 4.5 μm and 13 μm can be used. Additionally, for projects in Peru, its resistance to erosion must be 33 kΩ at 6 kV (table 1 IEC-60587), for projects outside of Peru its resistance to erosion must be 33 kΩ at 4.5 kV ( IEC-60587).
They are made of silicone rubber, firmly bonded to the cover through HTV vulcanization processes or molded as part of the cover, seamless, smooth and free of imperfections. The types of rubber to be used are completely free of ethylenepropylene- diene monomer (EPDM).
Sheath and sheds of composite long rod polymer Insulators are made of HTV silicone-rubber (VMQ - Vinyl-Methyl-Polysiloxane, with filler additives) free of EPDM or other natural origin rubbers.Silicone-rubber is HTV solid silicone type (High Temperature Vulcanized – solid silicone rubber).This type of silicone rubber is solid and vulcanizes at a high temperature (near 200ºC).
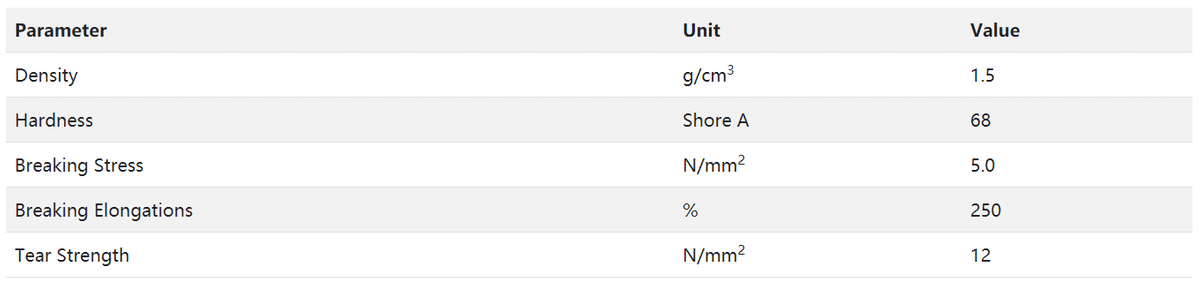
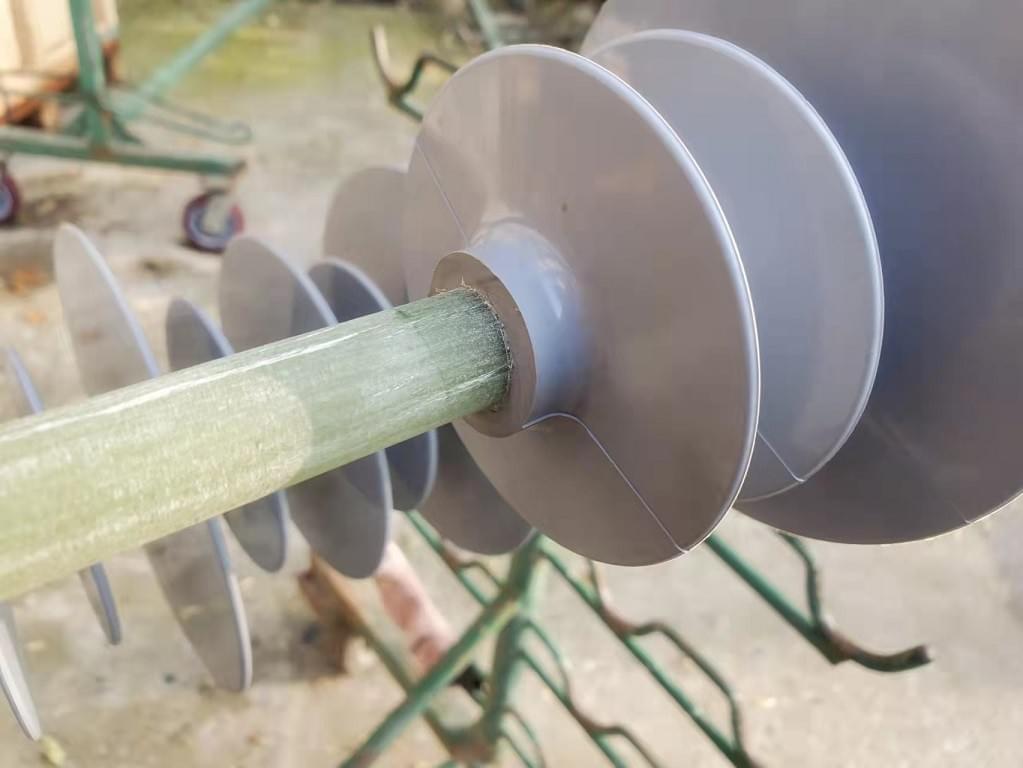
3.2 Core
The ECR fiberglass rod, which produced from epoxy resin and glass fiber, free of boron, cracks and bubbles, resistant to corrosion caused by acids and therefore to brittle breakage, constructed of a single piece, It is free of voids, foreign substances and manufacturing defects.
And the core has ability of high electrical integrity & high resistance to acid corrosion. Epoxy resin resistant to hydrolisys reinforced with glass fiber resistant to corrosion in order to transmit the mechanical stresses produced by conductors to the support and provides the necessary electrical insulation.The core is the component to bear mechanical load and has minimum tension strength at 1000Mpa.
3.3 End fittings
End metal fittings are hot-dip galvanized according to ASTM A153 standard, made of malleable cast iron or steel, and are designed in such a way as to reduce the electrical and mechanical stresses of the external cover. All metal parts are free of burrs, folds, fissures, cracks, blowholes, rough edges or any other imperfection that may impair the mechanical resistance of the insulator, the good condition of the connections, maintenance operations or cause the corona effect. The best performance has been observed in those where the external cover covers the protection ring of the hardware against electric field.
Mostly the end fittings are maded of hot dip galvanized forged steel, And the minimum galvanizing thickness for individual sample is 720g/m² (equivalent to 100 μm). The standards for end-fittings are as following:
- IEC 61466-1 Composite string insulator units for overhead lines with a nominal voltage greater than 1 000 V –Part 1: Standard strength classes and end fittings
- IEC 60120 Ball and socket couplings of string insulator units – Dimensions
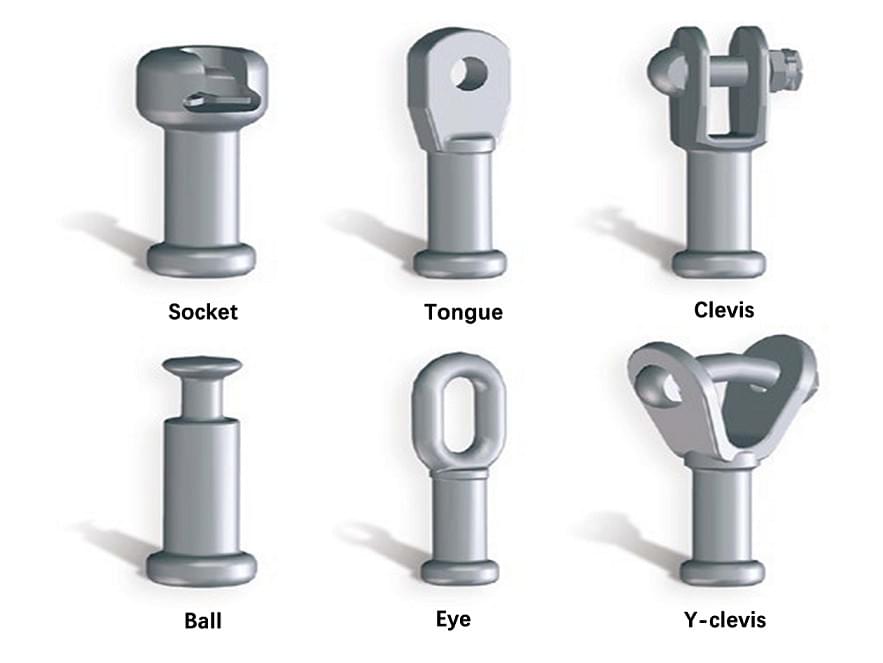
3.4 Corona rings
The number of rings will be indicated in the guaranteed technical characteristics; In any case, at the end of the line's side, it must always be provided with a metal ring of adequate diameter to control the corona effect, radio interference levels (RIV) and distribution of the electric field.
3.5 Interface
Interfaces between the outer shell and the core, and between the outer shell and external metal hardware, are smooth and free of voids, and have higher shear strength than the shell itself.
3.6 Sealing
The complete insulator have a permanent seal at the interface between the end fittings and the cover to prevent the ingress of moisture or outside material.
4. What is the advantages of composite long rod polymer insulators?
4.1 Easy to maintenance
Porcelain insulators have zero breakdown, zero detection and zero replacement problems, while long rod polymer insulators don’t have such problems. long rod polymer insulators nearly don’t require maintenance after installation, which greatly reduces maintenance costs.
Generally, the suspended porcelain insulator is an internal glue-installed structure, and the steel feet are embedded inside the porcelain ball head. Therefore, under the working voltage, the electric field strength is most concentrated at the steel feet. Adhesive is used for inner glue. Because the thermal expansion coefficients of porcelain and cement steel feet are different, when the porcelain insulator is subjected to changes in heat and cold, the difference in thermal expansion coefficient of each component will cause the porcelain parts to be subjected to greater compressive stress and shear stress, so the porcelain part is easy to crack or easy to break down and become a zero-value insulator. The long rod polymer insulator is a non-breakdown structure in mechanism, so there is no zero value problem.
4.2 Excellent stain resistance
The good anti-pollution flashover performance of the composite long rod polymer insulator is an important reason for its rapid development. Pollution flashover of insulators caused by surface contamination is the main threat to the safe operation of the power grid, and is also a decisive factor in the selection of power transmission line insulators. The surface of the porcelain insulator is a high-energy surface, which forms a continuous water film after being infiltrated by water. At the same time, it is subject to pollution and is prone to pollution flashover. Therefore, manual cleaning or smearing of silicone rubber paint should be adopted in daily operation.
According to statistics, Henan Power Grid of China has experienced two large-scale pollution flashover accidents in the past twenty years. In the large-scale pollution flashover accidents in 1990 and 2001, porcelain insulators flashed 104 times, accounting for 67%; glass insulators flashed 50 times, accounting for 32%; and composite long rod polymer insulator only flashed 1 time due to ice coating, accounting for 1 %.
The constituent material of the composite long rod polymer insulator is silicone rubber, and the surface of the shed and the sheath is a low-energy surface, so it has good hydrophobicity and hydrophobic migration. Even in a humid and dirty environment, a continuous water film will not be formed on the surface of the composite insulator shed, but only water droplets that are independent of each other, so the composite insulator has good pollution resistance. Although the hydrophobicity of composite insulators will deteriorate after a certain period of operation, its pollution resistance is still high compared to porcelain insulators.
4.3 Mechanical behavior
The axial tensile strength of the glass fiber mandrel used in composite insulators is very high, generally above 600MPa, and the tensile strength of the latest ECR acid-resistant mandrel is above 1000MPa, which is 5 - 10 times the strength of high-quality carbon steel. But the mass per unit length of the mandrel material is much lighter than both porcelain and steel. composite long rod polymer insulators can create very strong, lightweight products.
4.4 Anti-aging properties
Porcelain insulators have nearly a hundred years of operating experience and have strong anti-aging capabilities. For a long time after being put into operation, if zero damage does not occur, aging and replacement can be ignored. composite long rod polymer insulators belong to organic material insulators. Under the influence of the atmosphere, high and low temperature, ultraviolet rays, strong electric fields or other factors during operation, the organic materials in the shed sheath will age and deteriorate, resulting in poor insulation performance of composite insulators. Reduced, affecting the service life of composite insulators. However, from the current operating experience, the use of composite long rod polymer insulator can generally reach more than 10 years.
4.5 Economic performance
According to relevant calculations, whether it is a new line or an old line update, the use of composite long rod polymer insulator is more economical than porcelain insulators, and the later operation and maintenance workload of composite insulators is small, and zero-value detection is not required.
5. Color and Marking
The color of composite insulators is gray, red or as customers' requirements. Each insulator must be clearly and permanently marked, on the metal terminals, with the information indicated below:
- Maker -Xiangyang Guowang Composite Insulators Co., Ltd. or TONLY
- Year of manufacture
- Model
- Guaranteed and/or routine mechanical load
The marks are indelible and resistant to exposure to the elements.
6. Main products and others
Two fabrication processes are avaliable for manufacuturing of the silicone rubber sheds for long rod polymer insulators, molding process or assembling modules. Interference between the fiberglass rod, rubber housing are laid on a special adhesive that compound on the basis of silicone rubber and then vulcanized. This firmly bonds the rubber to the rod and bonds the rubber sheds to the rubber sheath so that the joint between sheds and sheath is stronger than the rubber.